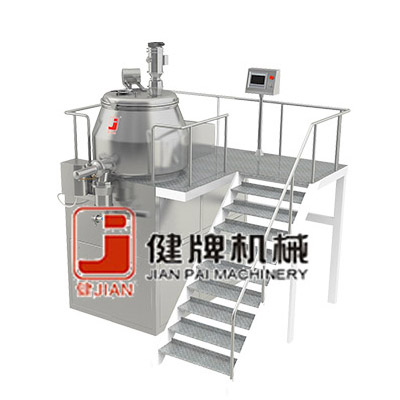
Model JHZ-D Series High-efficient Wet-process Granulator
- 我要分享:
Wet type granulators (other name: wet mixing granulator) of JHZ-D series is dedicated equipment used for the wet mixing granulating of powder, starch, adhesives and cream in food, pharmacy and chemistry industries. It is also used for the mixing and granulating of powder materials. This machine is newly designed on the basis of the old wet type granulator of JHZ-C series of our company, which better meets the technical requirements of solid preparation production. It is made of austenitic stainless steel and equipped with an operating platform, stairs and a safety fence. It has PLC control and frequency speed. Technical parameters can be designed according to the requirements of the users, with authentic reliable and original records. It can either work separately or together with a matched line. It completely conforms to the requirements of GMP of pharmacy industry.
By the adequate stirring from the bottom and the adhesives (or cream) sprayed by pressure, the materials in the cone container are mixed into a moist and soft state. With the cutting of the high-speed cutting tool on the side, the materials turn into uniform granules. The granules are straightened during the discharging of the material. By controlling the granule number, different granules can be made.
?The main barrel: The tangential structure between the cylinder and the cone is adopted, which is good for stirring materials. The angle between the stirring paddle and the parting tool is rationally designed, which ensures the optimized effect of mixing and granulating.
?The cutting tool is installed aslant to the straight wall of the barrel, which increases the contacting area between the parting tool and the materials and improves the uniformity of the granules. Besides, the aslant installation of the parting tool can prevent the materials from being sprayed to the cover of the barrel, avoiding the old problem of the traditional cutting.
?The efficiency of every new batch can be 4 to 5 times higher than that of the traditional technique.
?The whole granulating process of dry mixing and wet mixing is completed in a same airtight container, saving 25% of the adhesives and some drying time when compared with the traditional one.
?Operation controlling system: It is controlled by a computer with a touch screen, providing storage space for technical data of several processes. The parting tool adopts frequency speed, allowing free adjustment on its revolving speed, which meets the requirements of different granulating.
歡迎您發(fā)送【在線詢盤】!您有任何關(guān)于我司產(chǎn)品的建議及問題,可通過jp@cnjianpai.com給我們發(fā)郵件,也可通過此詢盤向我們反饋;我們將在24小時內(nèi)給您回復。(周一至周五9:00—17:30)
-
Model JHZ-D Series High-efficient Wet-process Granulator
-
Model JFL Series High-efficient Boiling Granulator
-
Model JFG-C Series High-efficient Boiling Drying Machine
-
Model JHZ-K Series Lab Wet-process Granulator
-
Model JYK Series Oscillating Granulator
-
Model JFZ/B Series Grinding Granulator
-
Model JZL Series Door Type Granulator